Patek Philippe - Dials
Unique in style, vital in purpose, the dial encompasses our whole perception of the watch. With hundreds of components beneath it, the dial is a delicate, thin sheet of precious material that interprets the tiny world of mechanisms that create time.
Through complex mechanisms working in harmony with beautiful design, every dial speaks to us. Creating a dial is a dedicated skill; venerable craftsmanship has been passed down through generations to create stunning, enduring pieces. Each dial model is unique. A dial for Patek Philippe takes four to six months of work with up to 200 operations, including decorative techniques. A systematic recipe, or routing, is created to ensure no stone is left unturned, and accuracy is paramount. There are over 600 possible routings, so the right one must be followed for each specific dial.
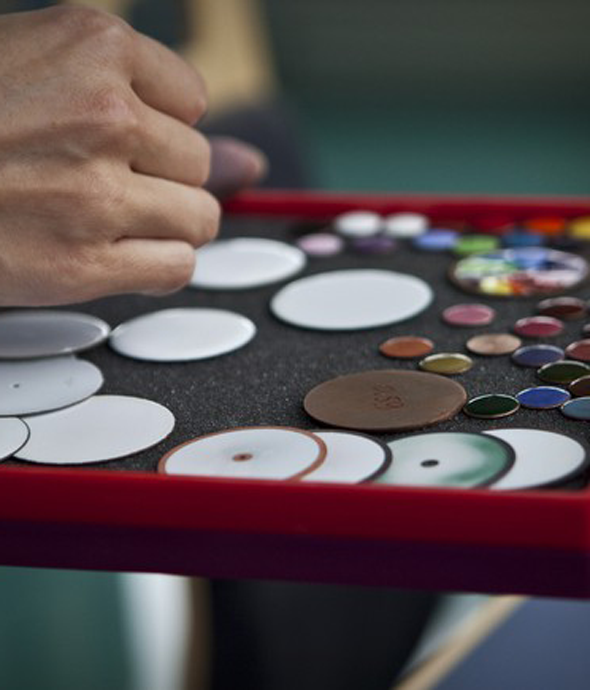
Enamelling
As one the most delicate and rare handcrafts, Patek Philippe use enamelling to decorate cases and dials. Coalescing powdered glass at extreme temperatures requires immense dexterity and patience to create results of incandescent beauty.
This specialised skill has been nurtured and preserved at Patek Philippe to create breathtaking pieces. Coloured glass or enamel pigments are ground to a fine powder and mixed with lavender oil. It is then meticulously painted onto the metal surface using a brush as fine as a single hair, then fired in a kiln at 850°C. The powdered glass or pigment melts to form a new surface that is fused to the metal base. Patek Philippe enamelling is built to endure generations of wear and tear, while creating a stunning display.

Guilloché
Traditional hand-guilloché techniques are used to engrave straight or circular grooves that are so fine, they are immensely smooth to the touch. The traversing lines of guilloché form a veneer of infinitely varied designs that sparkle in the light.
The straight lathe cuts lines that intersect at any angle, and rose lathes offer a richer variety of motifs with curved lines. Hand-guilloché artisans are rare, but with designs by Patek Philippe, the art is cherished and given the chance to flourish.
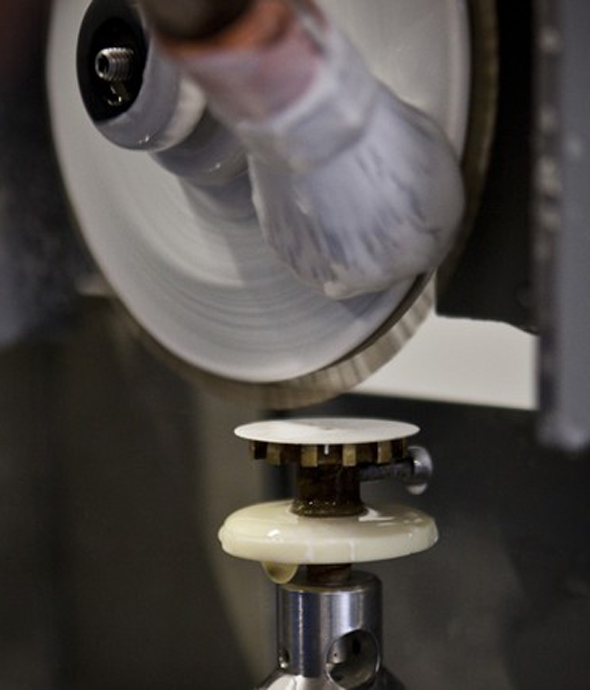
Decorations
These intricate operations enhance the dial with deep colour and fine detail. The craftsman uses one of four different techniques to achieve his masterpiece. Sunburst: metal bristles and an abrasive paste formed from natural rock create rays that expand from the centre to the edges, requiring precision and a steady hand. When completed, the dial will reveal a magnificent sunburst effect. Vertical satin-brushed: every bristle of the metal brush is exactly the same length and completely straight as the brush is drawn downward with expert care. Sand-blasting: the dial is positioned in a machine and powerfully blasted with crushed rock and water until stippled with a finely grained surface. Velvet finishing: sand-blasted for a matte surface, a cream of tartar is then applied for a felt finish.
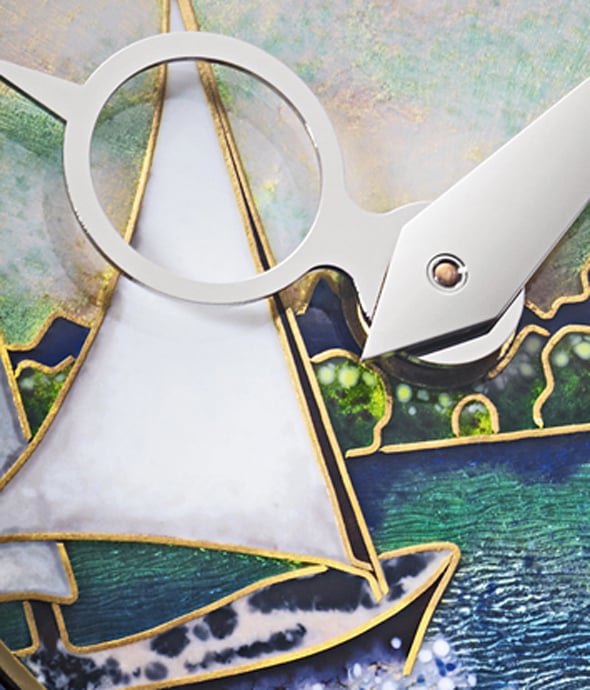
Painting and Varnishing
Dials are returned to the electroplating workshop, then immersed in chemical baths of different metallic shades to achieve a vast range of colours. After a second electroplating, the dials dazzle with their subtle new tone. Dials can be varnished with every colour imaginable. A clear, protective cellulose varnish is then applied to prevent oxidation. Varnishing must be carried out in a dedicated cubicle to prevent tiny particles of dust from sticking to the dial. Clothed in antistatic gear, the operator applies varnish twice over to achieve the perfect colour.
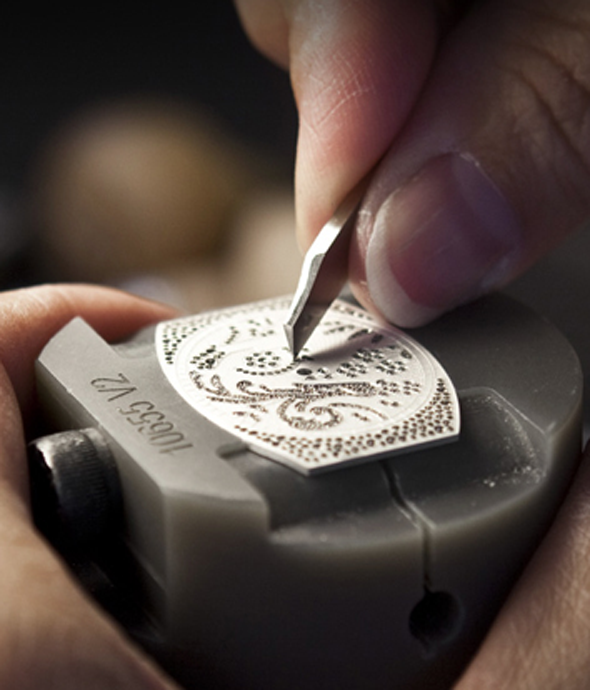
Gemsetting
All precious stones and gems must comply with the Patek Philippe Seal. From rubies and emeralds, to sapphires and diamonds, they must be of the utmost clarity. Diamonds must be of the internally flawless (IF) grade and the cut must match the international grades ‘excellent’ to ‘very good.’ Patek Philippe gems are always set by hand, and we never use adhesive. Whatever the design, the setter always considers the shape and particular character of each gem to accentuate its beauty.
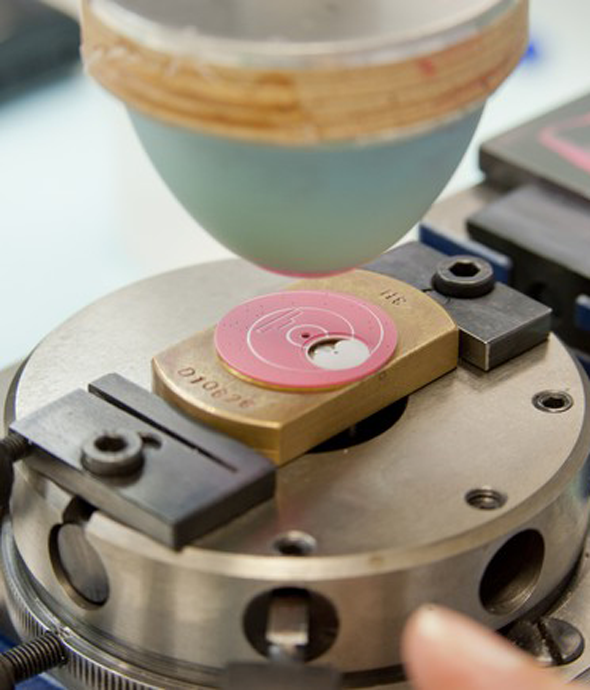
Décalque
Décalque is the delicate lithographic process where any printing design, such as numerals, are transferred onto the dial. Using ink on an engraved plate and a silicone cloth, any markings and inscriptions are put in place. This delicate procedure takes place in a white room to prevent dust particles from settling onto the design. The craftsman requires a steady hand and immense concentration. The job may need to be repeated several times to transfer all the inscriptions or colours.
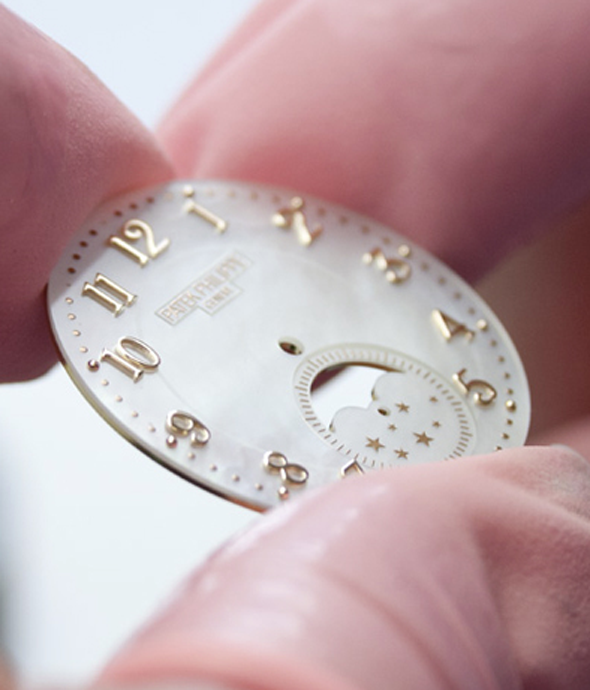
Numerals or Indexes
All Patek Philippe hour markers are 18k gold. They are transfer printed by hand or created using round or baguette-cut diamonds. Hour markers require extensive work and have over a hundred different steps consisting of swaging, faceting and setting appliques.
These processes include complex machinery fitted with sharp diamond tools. Hour markers are either cut with small, planed surfaces at the edges, flat diamond-polished, or chamfered, then given a distinct final polish. The last operation on the dial is setting the hour marker appliques carried out entirely by hand. Applied numerals and markers are made of gold and firmly secured to guarantee supreme durability.
Discover more about Patek Philippe
Patek CLP Page
Contact us